Aluminum Die Casting for Medical Devices
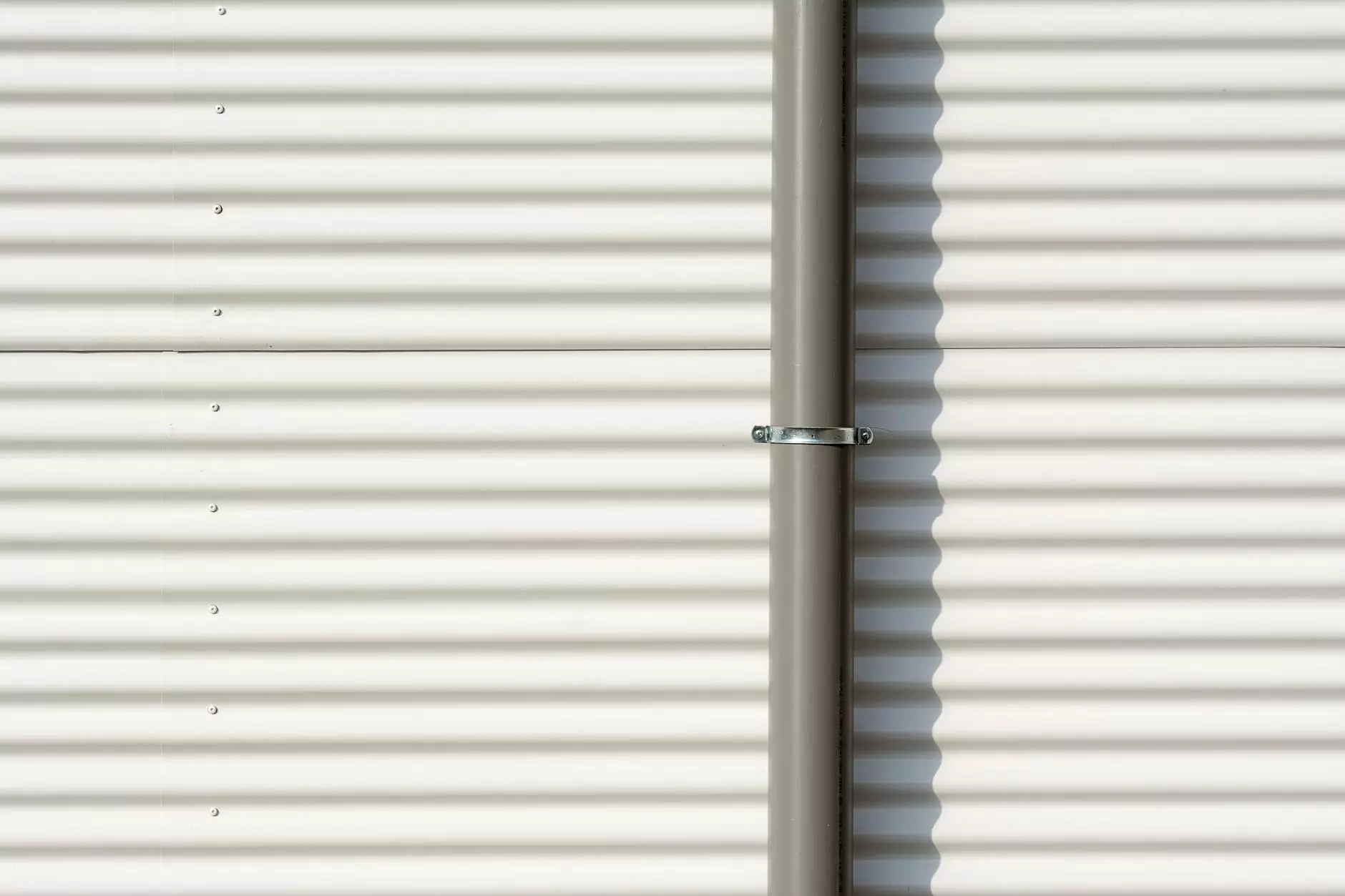
Introduction
Welcome to Wetron Industrial, a leading provider of high-quality aluminum die casting services for various industries including Home & Garden and Appliances. In this article, we will explore the advantages and applications of aluminum die casting for medical devices. As an expert in the field, we aim to provide you with valuable insights and information to help you understand how this advanced manufacturing process can benefit your business.
What is Aluminum Die Casting?
Aluminum die casting is a widely adopted manufacturing process that involves injecting molten aluminum into a steel mold, also known as a die. The molten metal is forced into the die cavity under high pressure, ensuring precise and intricate detailing of the final product. Once cooled and solidified, the die is opened, and the newly formed aluminum component is removed, ready for further processing.
The Advantages of Aluminum Die Casting
Aluminum die casting offers numerous advantages, making it a popular choice for manufacturing medical devices. Let's take a closer look at some of the key benefits:
1. Lightweight and Durable
Medical devices require materials that are both lightweight and durable. Aluminum, with its exceptional strength-to-weight ratio, fits this requirement perfectly. Aluminum die castings provide the necessary strength and durability while keeping the overall weight of the devices low. This lightweight nature allows for easier handling and portability of medical devices, enhancing user experience and convenience.
2. Precision and Complex Shapes
Aluminum die casting excels in producing components with intricate shapes and complex geometries. The high-pressure injection process ensures excellent dimensional accuracy and repeatability, allowing for the creation of precise medical device components. This level of detail is crucial in the medical field, where even the smallest variations can have significant impacts on functionality and performance.
3. Cost-Effective Production
Efficiency and cost-effectiveness are vital considerations in medical device manufacturing. Aluminum die casting offers excellent production efficiency with its ability to create net-shape components, minimizing the need for additional machining or assembly. The high-speed production capabilities of die casting help reduce labor and production costs, resulting in a cost-effective manufacturing process for medical devices.
4. Surface Finishing Options
Medical devices often require specific surface finishes to meet aesthetic and functional requirements. Aluminum die casting allows for a wide range of surface finishing options, including powder coating, anodizing, and painting. These finishes improve the visual appeal, corrosion resistance, and overall durability of the medical device while ensuring compliance with industry standards and regulations.
5. Excellent Electrical Conductivity and Thermal Properties
Some medical devices rely on electrical conductivity and efficient heat dissipation to function optimally. Aluminum, being an excellent conductor of electricity and having superior thermal properties, makes it an ideal material for the production of medical devices. Components manufactured through aluminum die casting provide excellent electrical conductivity and efficient heat dissipation, ensuring optimal performance and reliability.
Applications of Aluminum Die Casting in Medical Devices
Aluminum die casting finds extensive applications in the medical device industry. Here are some common areas where this manufacturing process is utilized:
1. Surgical Instruments and Tools
The production of surgical instruments and tools requires precision, durability, and corrosion resistance. Aluminum die casting enables the creation of these critical components with the desired properties, ensuring high-quality and reliable tools for medical professionals.
2. Imaging and Diagnostic Equipment
Imaging and diagnostic equipment, such as ultrasound machines and X-ray devices, often incorporate aluminum die castings in their structural and functional components. The lightweight nature of aluminum allows for portable imaging devices without compromising on durability and reliability.
3. Prosthetics and Orthotics
Aluminum die casting plays a crucial role in the manufacturing of prosthetics and orthotics. The ability to produce complex shapes and lightweight components makes it an ideal choice for creating customized and comfortable solutions for patients in need of artificial limbs or orthopedic supports.
4. Respiratory and Life Support Devices
Respiratory and life support devices, such as ventilators and oxygen concentrators, often incorporate aluminum die castings due to their lightweight and durable nature. These components help ensure the reliability and effectiveness of life-saving equipment.
Conclusion
Aluminum die casting offers significant advantages in the manufacturing of medical devices for the Home & Garden and Appliances industries. From lightweight and durable components to cost-effective production and excellent surface finishing options, the benefits are numerous. Wetron Industrial is committed to providing high-quality die casting services, leveraging the advantages of aluminum die casting to meet the unique needs and specifications of our clients in the medical field.