Understanding Silicone Injection Molding: Transforming Electronics and Medical Supplies
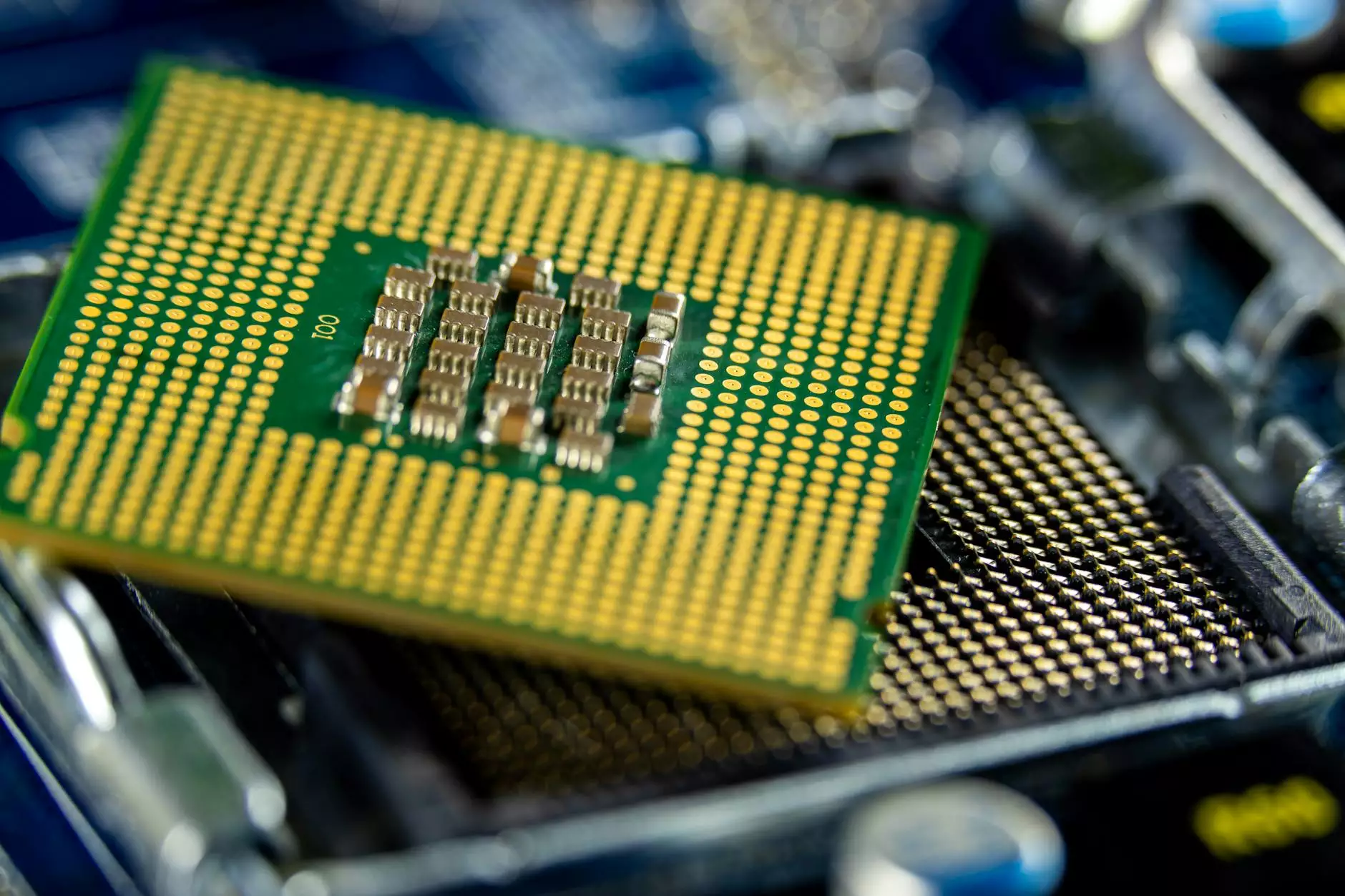
In the realms of electronics and medical supplies, the demand for innovative manufacturing techniques continues to rise. One such technique that stands out is silicone injection molding. This process not only enhances production efficiency but also contributes to the durability and functionality of products across various industries.
What is Silicone Injection Molding?
Silicone injection molding is a manufacturing process where liquid silicone rubber (LSR) is injected into a pre-designed mold cavity to create parts or products. This technique offers remarkable flexibility in design and can produce intricate components with tight tolerances. The silicone material used is renowned for its high heat resistance, flexibility, and longevity, making it an ideal choice for both electronics and medical applications.
The Process of Silicone Injection Molding
The silicone injection molding process involves several stages:
- Material Preparation: High-quality silicone rubber, often in liquid form, is prepared and heated to make it mold-ready.
- Injection: The prepared liquid silicone is injected into a precisely crafted mold under high pressure.
- Curing: Once injected, the silicone undergoes a curing process, where it solidifies to take the shape of the mold.
- Cooling: After curing, the mold is cooled down, allowing for the extracted product to stabilize.
- Finishing: The finished silicone parts may undergo additional processing steps such as trimming and surface treatment.
Benefits of Silicone Injection Molding
The choice of silicone injection molding offers numerous benefits that are particularly advantageous in the electronics and medical sectors:
- Precision and Detail: Silicone injection molding allows for the production of highly complex geometries with exceptional precision.
- Durability: Silicone products exhibit excellent resistance to temperature extremes, UV light, and physical wear, making them ideal for long-lasting applications.
- Versatility: It is suitable for various grades of silicone, including those with specialized properties for specific applications.
- Rapid Production: This process significantly speeds up manufacturing times, enabling quicker time to market for new products.
- Cost-Effective: Although the initial tooling costs can be high, the lower per-unit manufacturing costs make it economically feasible for large production runs.
Applications in Electronics
The electronics industry has embraced silicone injection molding for different applications:
- Keypads and Switches: The flexibility and tactile properties of silicone make it an excellent choice for producing keypads and switches.
- Sealing Components: Silicone's resistance to environmental conditions allows it to be used in sealing gaskets and O-rings, ensuring longevity and reliability in electronic devices.
- Insulation and Potting: Silicone provides excellent electrical insulation, making it ideal for potting compounds to encase sensitive electronic components.
Applications in Medical Supplies
Silicone injection molding plays a pivotal role in the medical industry:
- Medical Devices: Many medical devices, including syringes, catheters, and valves, benefit from silicone's biocompatibility and durability.
- Testing Devices: Silicone components are often used in diagnostic devices due to their precision and ability to maintain sterility.
- Wearable Health Tech: The rise of wearable technology in healthcare often uses silicone for bands and housings due to its comfort and resilience.
Innovation and Future Trends
As the demand for silicone injection molding grows, so do the innovations surrounding it. Companies like Nolato are leading the charge by integrating advanced technologies such as:
- Automation: Incorporating automation in the manufacturing process reduces labor costs and increases production capacity.
- 3D Printing Prototyping: 3D printing technologies are enabling rapid prototyping of silicone products, speeding up research and development phases.
- Smart Manufacturing: The Internet of Things (IoT) is allowing manufacturers to collect data for better process control and optimization, which enhances overall product quality.
Choosing the Right Partner for Silicone Injection Molding
Selecting a reliable manufacturer for silicone injection molding is crucial for ensuring quality and innovation. When considering a partner, look for the following qualifications:
- Experience and Expertise: Evaluate their experience in silicone injection molding, especially in your industry sector.
- Technology and Equipment: Ensure they use state-of-the-art machinery and techniques for optimal results.
- Quality Assurance: Look for manufacturers with a stringent quality control program to ensure product reliability.
- Custom Solutions: The ability to provide tailored solutions for unique projects is essential.
The Environmental Impact of Silicone Injection Molding
As industries evolve, so too does the focus on sustainability. The environmental impact of silicone injection molding is an increasing concern:
- Recyclability: Silicone is a recyclable material, and manufacturers are finding ways to repurpose scrap silicone to reduce waste.
- Energy Efficiency: Improvements in molding technologies are helping to reduce energy usage in the manufacturing process.
- Non-toxic Properties: Many silicone materials are free from harmful chemicals, making them safer for medical applications and reducing environmental harm.
Conclusion
In summary, silicone injection molding is a transformative process that is reshaping the electronics and medical supplies industries. With its numerous advantages such as precision, durability, and versatility, it has become an integral component of modern manufacturing. As trends continue to evolve, companies like Nolato remain at the forefront of innovation, ensuring that businesses can meet market demands while maintaining sustainability and quality. The future looks bright for silicone injection molding, and its role in producing high-quality products will only expand as technology advances.