Injection Molded Plastic Manufacturers: Pioneers of Innovation in Modern Industry
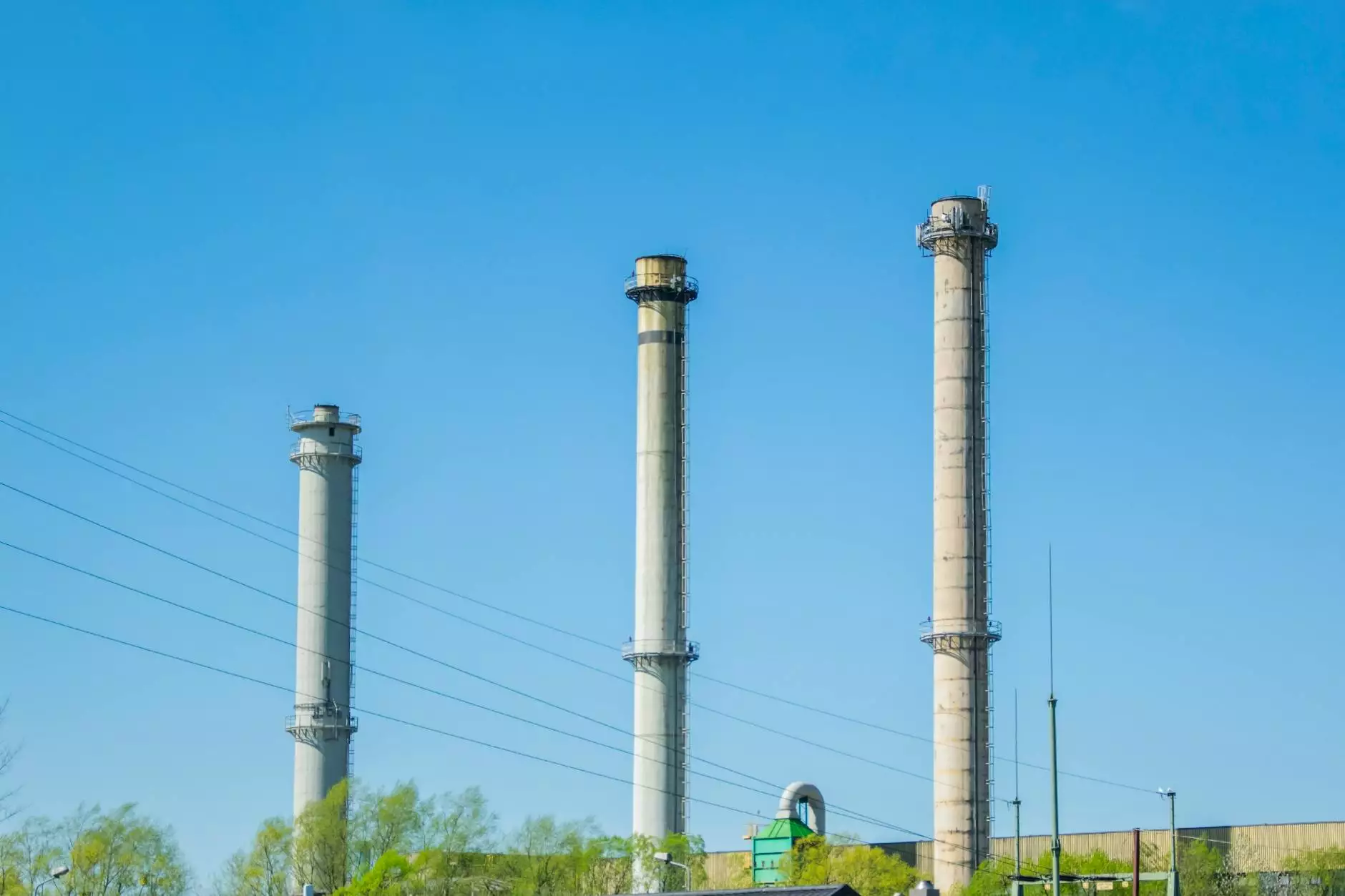
In today's fast-paced world, where efficiency and technological advancement reign supreme, injection molded plastic manufacturers stand out as vital contributors to diverse sectors and applications. This article delves into the essential roles these manufacturers play, the processes they employ, and their impact on global industries.
The Fundamentals of Injection Molding
Injection molding is a sophisticated process that transforms raw plastic materials into desirable molded products. The process involves several critical steps:
- Material Selection: The journey begins with selecting the right type of plastic resin, which can significantly affect the outcome of the final product.
- Heating and Melting: The chosen resin is then heated until it melts, becoming pliable enough to be inserted into a mold.
- Injection: The molten plastic is injected into a mold cavity at high pressure, allowing it to take the shape of the mold.
- Cooling: After injection, the material cools and solidifies, forming the final product.
- Ejection: Once cooled, the finished part is ejected from the mold, ready for post-processing or assembly.
The Benefits of Choosing Injection Molded Plastic
Injection molded plastic offers numerous advantages, establishing it as a favored choice among manufacturers:
- Cost Efficiency: High-volume production utilizing injection molding significantly reduces the cost per unit, making it economically viable for large-scale manufacturing.
- Consistency and Precision: The process allows for exceptional accuracy in dimensions and shapes, resulting in uniform products that meet high-quality standards.
- Material Versatility: A wide range of thermoplastic and thermosetting materials can be used in injection molding, allowing manufacturers to select the perfect resin for their applications.
- Rapid Production: The speed of the injection molding process means manufacturers can meet tight deadlines, ensuring timely delivery to clients.
- Reduced Waste: The efficient nature of the process leads to minimal material waste, contributing to sustainable manufacturing practices.
Applications of Injection Molding Across Industries
Injection molded plastic products are omnipresent, playing a crucial role in various industries, including:
Aerospace and Automotive
The aerospace and automotive sectors rely heavily on injection molding for lightweight, durable components that can withstand extreme conditions while adhering to strict safety standards.
Consumer Goods
From household items to electronics, consumer goods manufacturers use injection molding to produce items that are not only functional but also aesthetically pleasing, sporting intricate designs and vibrant colors.
Medical Devices
The medical industry necessitates precision and compliance with regulatory standards. Injection molding is employed to create everything from syringes to complex instruments, ensuring both safety and effectiveness.
Packaging
Packaging solutions, such as containers and closures, are often produced using injection molding to provide durability while also maintaining cost-effectiveness.
Choosing the Right Injection Molded Plastic Manufacturer
Selecting the right injection molded plastic manufacturer is imperative for ensuring the success of your product. Here are several key factors to consider:
- Experience and Expertise: Choose manufacturers with a proven track record and expertise in your specific industry. An experienced partner will understand the nuances of material selection and production processes.
- Technology and Equipment: Advanced machinery can enhance production efficiency and product quality. Manufacturers leveraging the latest technology can provide better precision and adaptability.
- Quality Assurance: Ensure the manufacturer has stringent quality control measures in place. Certifications like ISO 9001 can be indicative of their commitment to quality.
- Customer Support: A responsive manufacturer that offers excellent support can help address concerns during the project lifecycle, making collaboration more effective.
- Customization Capabilities: Depending on your needs, a manufacturer should be capable of providing tailored solutions, including custom mold designs and materials.
DeepMould.net: Leading Professionals in Injection Molding
At DeepMould.net, we pride ourselves on our commitment to excellence in the realm of injection molded plastic manufacturers. Our team of experts is dedicated to leveraging cutting-edge technology to deliver innovative solutions for our clients.
Why Choose DeepMould.net?
When you partner with us, you can expect:
Innovative Design Solutions
Our design team collaborates closely with you to develop product concepts that align with your vision while optimizing manufacturability and functionality.
Robust Production Processes
With state-of-the-art machinery and skilled personnel, we assure a seamless production process that meets the highest industry standards.
Commitment to Sustainability
We are dedicated to sustainable practices, utilizing efficient processes and recyclable materials whenever possible, to minimize our environmental footprint.
Comprehensive Support
From initial consultation to post-production, our team provides ongoing support, ensuring all your queries are addressed and your expectations are surpassed.
The Future of Injection Molding
As industries continue to evolve, so too does the injection molding process. Advances in technology, such as automation and artificial intelligence, are set to enhance precision manufacturing and operational efficiency. Emerging materials, including bio-based plastics, are also paving the way for more sustainable production practices.
Innovations Shaping the Industry
Some of the critical innovations in injection molding include:
- 3D Printing Integration: The combination of 3D printing and injection molding allows for rapid prototyping, enabling manufacturers to create molds more efficiently and cost-effectively.
- Smart Manufacturing: IoT integration provides real-time monitoring and data analytics, optimizing production processes and leading to greater efficiency.
- New Material Development: Research into novel materials continues to expand the range of possibilities for injection molding, allowing for greater performance and sustainability.
Conclusion
Injection molded plastic manufacturers are at the forefront of innovation, driving advancements across various industries. Their ability to create high-quality, customizable products efficiently and cost-effectively makes them invaluable allies in product development. As we look towards the future, the role of injection molded plastics will only grow, empowered by technological advancements and a focus on sustainability.
For unparalleled expertise and support in injection molding, explore how DeepMould.net can elevate your manufacturing needs today.