The Crucial Role of **Shear Stress** in Modern Engineering
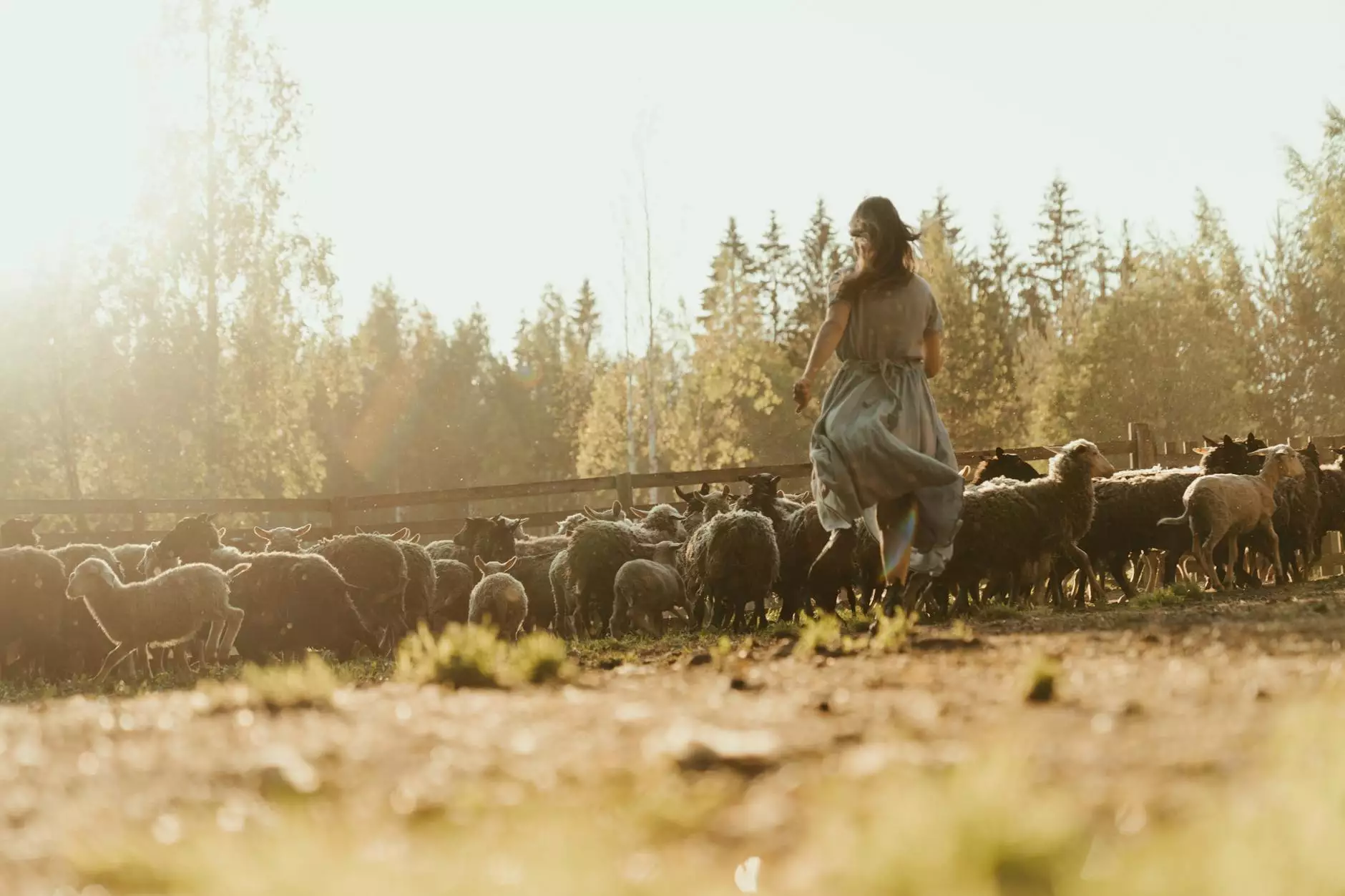
In the field of engineering, understanding fundamental concepts is vital for the successful execution of projects that range from auto repair to complex structural engineering tasks. One such paramount principle is shear stress. This article delves deeply into what shear stress is, its implications in various engineering applications, and why mastering it can set your projects apart and ensure safety and efficiency. As a leading provider of engineering services, Michael Smith Engineers emphasizes the importance of grasping this concept in our multifaceted projects.
What is Shear Stress?
Shear stress is defined as the force per unit area that acts parallel to the surface of a material. It is represented by the formula:
τ = F/A
where τ is the shear stress, F is the applied force, and A is the area over which the force acts. Understanding this principle is crucial for engineers because it helps them predict how materials will behave under various loads, especially in scenarios where forces act tangentially to a surface.
The Importance of Shear Stress in Engineering Applications
Shear stress plays a pivotal role in numerous engineering disciplines. Here are some key applications in which understanding shear stress is essential:
1. Auto Repair
- Chassis Integrity: The chassis of a vehicle is subjected to various forces during operation. Mechanics must understand how shear stress affects weld points and joints to ensure safety and durability.
- Suspension Systems: The tension and compression experienced by suspension components create shear stress that can lead to premature failure if not properly accounted for.
- Brake Systems: Understanding shear stress is crucial for designing brake components that withstand the forces during braking without compromising integrity.
2. Farm Equipment Repair
- Implement Strength: Agricultural machinery parts are often exposed to significant shear forces. Knowledge of shear stress helps repair technicians understand the wear patterns and potential failure points in components such as plows and cultivators.
- Pivot Points: The pivot points of equipment must be designed to handle shear forces to prevent equipment failure during operation.
- Material Selection: The choice of materials for different parts of farm equipment involves understanding the shear stress they can withstand, ensuring long-term reliability and performance.
3. Structural Engineering
- Load Analysis: Structural engineers perform load analysis to calculate the shear stress on beams, columns, and other structural elements. This is vital for ensuring that structures can safely support anticipated loads.
- Connection Design: Joints and connections in frameworks must be designed to resist shear forces, and a thorough understanding of shear stress is critical in this context.
- Material Failure: Engineers must predict when a material will fail due to excessive shear stress, preventing structural collapse and ensuring safety.
How Shear Stress Influences Material Selection
When designing components in engineering applications, material selection is crucial, and shear stress is a significant factor in this process. Different materials behave differently under shear forces:
- Metals: Commonly used for their excellent shear strength, but different alloys have varied rest performance under shear stress. Engineers must choose the right alloy for each application.
- Plastics: Certain plastics can endure considerable shear stress but are often limited in load-bearing applications.
- Composites: These materials can be engineered to possess superior shear strength, making them ideal for specific applications in both automotive and structural engineering.
Shear Stress vs. Other Types of Stress
It’s essential to differentiate shear stress from other stress types that materials experience, such as tensile and compressive stress:
- Tensile Stress: This occurs when a material is subjected to pulling forces. It is calculated using a similar formula involving force and area but applies to axial forces rather than side forces.
- Compressive Stress: Opposite to tensile stress, compressive stress happens when materials are subjected to pushing forces. Effective designs must take all these types of stress into account to ensure structural integrity.
Calculating Shear Stress: Practical Examples
Understanding how to calculate shear stress is fundamental for engineers. Below are two practical examples:
Example 1: Shear Stress in a Beam
Consider a rectangular beam subjected to a lateral load. If the load is 2000 N and the width of the beam is 50 mm, the shear stress can be calculated as follows:
τ = F/A = 2000 N / (50 mm * 1000 mm) = 0.04 N/mm² or 40 kPa
Example 2: Shear Stress in Metal Joints
If a metal plate experiences a shear force of 500 N and has an effective shear area of 25 mm², the shear stress can be calculated:
τ = F/A = 500 N / 25 mm² = 20 N/mm²
Shear Stress in Design Considerations
When designing components and systems, engineers often perform a concept called shear stress analysis to ensure that all elements will perform safely under expected loads. Key considerations include:
- Safety Factors: Engineers rarely design components to operate right at their maximum shear stress limits. A safety factor (usually 1.5 to 3 times the expected load) is incorporated.
- Testing and Validation: Real-world testing is essential. Physical tests that measure shear stress can provide invaluable data on whether a design will hold up under realistic conditions.
- Monitoring and Maintenance: For existing structures, monitoring changes in shear stress over time can help engineers anticipate maintenance needs before critical failures occur.
Advancements in Shear Stress Measurement Techniques
Technological advancements have made measuring shear stress more accessible and accurate. These methods include:
- Strain Gauges: These sensors can be affixed to materials to measure deformation directly, allowing engineers to calculate shear stress in real-time.
- Finite Element Analysis (FEA): This computational technique enables engineers to model how materials will react under different loads, predicting shear stress distribution throughout a component.
- 3D Printing for Prototypes: Rapid prototyping using 3D printing can help test shear performance before full-scale production.
Conclusion: Mastering Shear Stress for Engineering Excellence
In conclusion, a deep understanding of shear stress is essential for engineers across all disciplines, including auto repair, farm equipment repair, and structural engineering. The ability to calculate, analyze, and design for shear stress not only improves safety and durability but also enhances overall project efficiency.
At Michael Smith Engineers, we recognize the intricacies involved in managing shear stress and its implications in our services. Our commitment to excellence hinges not just on understanding these critical principles but also on applying them effectively to deliver outstanding projects. By mastering shear stress, we ensure our engineering solutions meet the highest standards of reliability and performance.
Understanding shear stress may seem like a complex undertaking, yet it is one that is ultimately rewarding, offering significant returns on investment in safe, reliable, and efficient engineering practices.