Injection Molding Shops: Revolutionizing Plastic Manufacturing
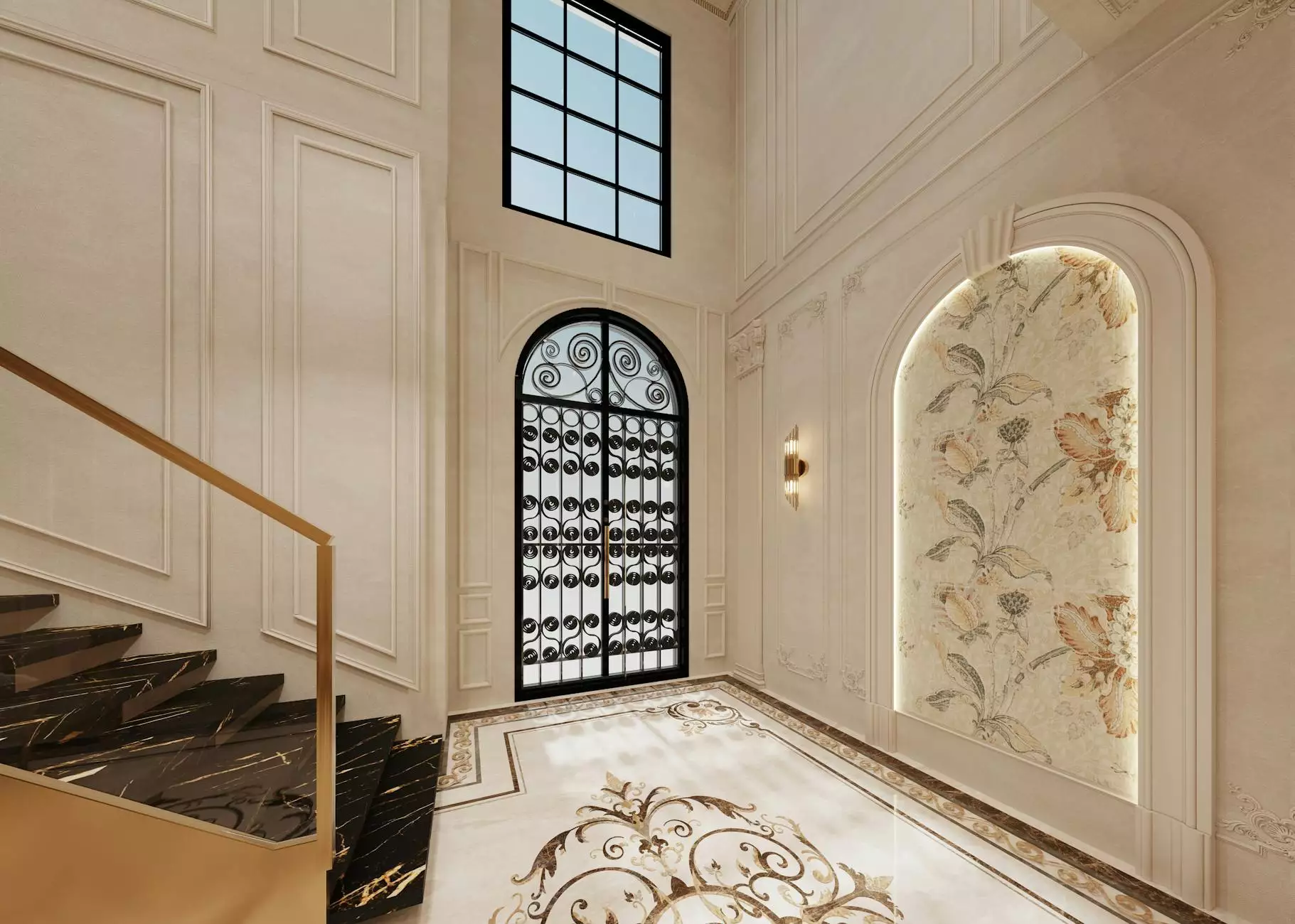
What Are Injection Molding Shops?
Injection molding shops are specialized facilities that manufacture plastic products by melting plastic resins and injecting them into molds. This process allows for the creation of highly intricate and precise components used in various industries, from automotive to consumer goods.
At Hanking Mould, we pride ourselves on being leaders in this sector, providing superior plastic mold making and manufacturing services. Our expertise enables businesses to access a range of high-quality molded parts tailored to their specifications.
The Injection Molding Process: A Step-by-Step Guide
The injection molding process is a critical operation within injection molding shops. Here’s a detailed overview of the steps involved:
- Material Selection: The first step involves choosing the appropriate plastic resin, which can range from thermoplastics to thermosets, depending on the final product's needs.
- Granulation: The selected plastic is typically in granular form. This granule is transformed into a flowable mass during the melting process.
- Melting: The granules are fed into an injection molding machine and heated to a molten state, allowing for easy injection into the mold.
- Injection: The molten plastic is injected under high pressure into a pre-shaped mold. This step is crucial for achieving the desired item shape accurately.
- Cooling: After injection, the mold is cooled, solidifying the plastic into the final product shape.
- Demolding: Once cooled, the mold opens, and the finished part is ejected from the mold cavity.
- Finishing Touches: Additional processes, such as trimming, finishing, and assembly, may follow to enhance the product's quality and usability.
Benefits of Using Injection Molding Shops
Injection molding shops like Hanking Mould offer numerous advantages that make them the go-to choice for manufacturers across different sectors. Here are some key benefits:
- High Production Efficiency: Once the molds are designed and produced, injection molding can rapidly produce large quantities of parts, significantly reducing lead times.
- Design Flexibility: Injection molding allows for complex designs and fine details that may be difficult or impossible to achieve with other manufacturing methods.
- Consistent Quality: Automated processes minimize human errors, ensuring that each part produced meets exact specifications and quality standards.
- Cost-Effectiveness: Although initial mold creation may be expensive, the ability to mass-produce at low cost makes it economically viable for large production runs.
- Material Variety: Injection molding shops can work with a vast array of materials, including plastics, elastomers, and even metals, enabling diverse product applications.
The Role of Hanking Mould in Injection Molding
As a leading plastic injection mould manufacturer, Hanking Mould plays a crucial role in the injection molding landscape. Our facilities are equipped with state-of-the-art technology, ensuring precision and efficiency in every phase of the molding process.
We specialize in:
- Custom Mold Design: Our engineering team works closely with clients to develop molds that meet their unique product requirements.
- Prototype Development: Before full-scale production, we offer prototyping services to ensure that designs work effectively in practical applications.
- Material Recommendations: Our experts suggest the best materials for your needs, considering factors such as durability, flexibility, and cost.
- Quality Assurance: We maintain strict quality control measures throughout the production process, ensuring that each component meets industry standards.
Industry Applications of Injection Molding
Injection molding is a versatile technology that finds applications in various industries. Here’s how different sectors leverage the capabilities of injection molding shops:
1. Automotive Industry
The automotive industry relies heavily on injection molding for manufacturing components such as dashboards, bumpers, and interior fixtures. Injection molding allows for innovative designs that improve vehicle performance and aesthetics.
2. Consumer Products
From household items to electronic gadgets, consumer products benefit greatly from injection molding's ability to produce high-quality, durable components at scale. Companies can create engaging designs that appeal to consumers.
3. Medical Devices
Injection molding is vital in producing precise and hygienic components for medical devices. The ability to produce complex geometries and use biocompatible materials ensures that products meet stringent health standards.
4. Packaging
In the packaging industry, injection molding creates containers, closures, and dispensers that are both functional and aesthetically pleasing, catering to modern branding needs.
5. Electronics
Injection molded parts form the basis of many electronic devices, from casings to internal components, providing protection and facilitating the assembly of complex electronics.
Environmental Considerations in Injection Molding
As awareness of environmental issues grows, injection molding shops are adapting their practices to become more sustainable. Here are some ways the industry is working towards environmental responsibility:
- Recycling Materials: Many injection molding shops are incorporating recycled plastics into their production processes, thus reducing the need for virgin materials.
- Energy Efficiency: Modern machines are being designed to consume less energy, which not only lowers costs but also minimizes their environmental footprint.
- Reducing Waste: Implementing lean manufacturing techniques helps in reducing waste generation during production.
- Biodegradable Plastics: The use of biodegradable materials is on the rise, allowing companies to produce products that can minimize environmental impact after disposal.
The Future of Injection Molding Shops
The injection molding industry is evolving rapidly, influenced by advancements in technology and changing consumer demands. Here are some trends shaping the future:
1. Automation and Industry 4.0
Many injection molding shops are adopting automation technologies, such as robotics and IoT (Internet of Things) devices. This shift allows for more efficient production, precise quality control, and reduced labor costs.
2. Advanced Materials
The development of new materials, including smart plastics and composites, is expanding the capabilities of injection molding shops. These materials provide additional functionality, making them suitable for high-performance applications.
3. Customization and On-Demand Manufacturing
As consumer preferences shift towards personalized products, injection molding shops are leveraging technology to offer customized solutions quickly and efficiently, meeting market demands in real-time.
4. Additive Manufacturing Integration
Combining traditional injection molding with additive manufacturing techniques can enhance prototyping and mold creation, leading to faster production cycles and the ability to test designs before full-scale production.
Conclusion
Injection molding shops are at the forefront of modern manufacturing, offering unparalleled precision, efficiency, and flexibility. With companies like Hanking Mould leading the way, the future of injection molding promises to be bright, innovative, and environmentally conscious.
As the demand for plastic products continues to grow, understanding the intricacies of injection molding can empower businesses to make informed decisions and capitalize on the benefits of this remarkable process.