Understanding Injection Plastic Molding: A Comprehensive Guide
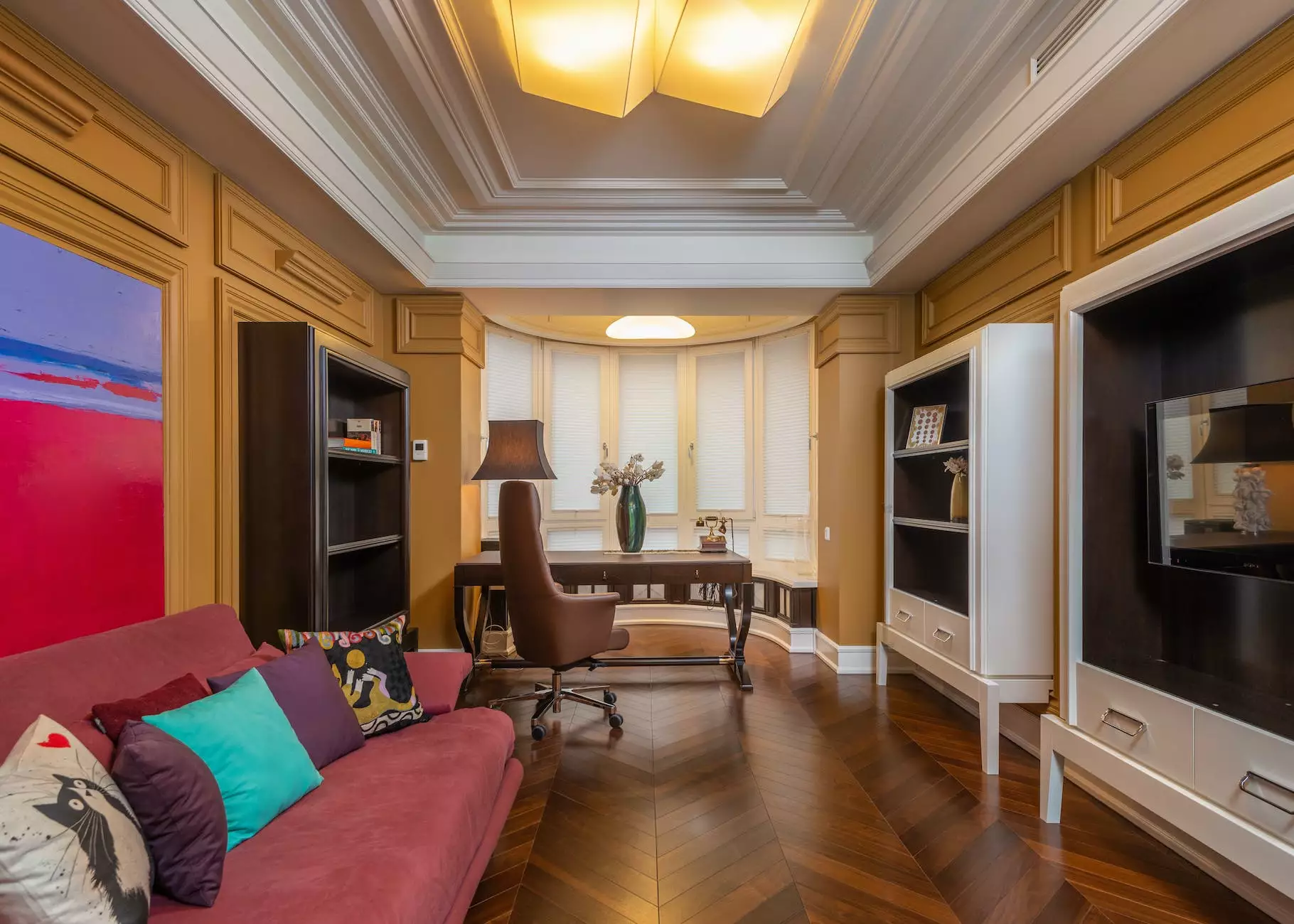
In the realm of modern manufacturing, injection plastic molding stands as a pivotal process that has revolutionized the production of plastic parts. This technique has proven invaluable for various industries, offering efficiency, precision, and versatility. This article explores the intricacies of injection plastic molding, its benefits, applications, and how it integrates with the field of metal fabricators.
What is Injection Plastic Molding?
Injection plastic molding is a manufacturing process used to produce parts by injecting molten material into a mold. This technique is primarily employed in producing plastic components, providing high precision and repeatability. The process has become a standard in the manufacturing industry due to its ability to produce complex shapes and tolerances with minimal waste.
The Process of Injection Plastic Molding
The injection plastic molding process involves several key stages:
- Clamping: The mold is secured in a clamping unit where it is tightly closed to withstand the injection pressure.
- Injection: Plastic pellets are heated and melted, then injected under high pressure into a mold cavity, filling it completely.
- Cooling: The injected material cools and solidifies within the mold, taking the shape of the design.
- Opening: Once cooled, the mold is opened to eject the formed part.
- Finishing: The product may go through additional processes such as trimming or surface finishing.
Benefits of Injection Plastic Molding
Businesses engaging in injection plastic molding reap numerous advantages:
- Cost Efficiency: High production rates mean that the cost per unit decreases significantly as quantities increase.
- Rapid Production: The process allows for the quick manufacturing of large volumes of parts, meeting market demands efficiently.
- Precision and Repeatability: Injection molding can produce parts with intricate designs and tight tolerances consistently.
- Material Versatility: A wide variety of thermoplastics can be used, from flexible materials to rigid ones, enhancing design possibilities.
- Reduced Waste: Compared to other manufacturing methods, injection molding minimizes wastage of materials.
Applications of Injection Plastic Molding
The applications of injection plastic molding span across multiple industries:
Consumer Products
From household items to complex electronic casings, consumer products benefit greatly from injection molding due to its ability to create aesthetically pleasing and functional designs.
Automotive Industry
In the automotive sector, parts such as dashboards, door panels, and bumpers are commonly manufactured using this technique, contributing to weight reduction and design flexibility.
Medical Devices
The precision required in medical device manufacturing makes injection plastic molding essential. It is used for producing components in syringes, IV bags, and surgical instruments.
Industrial Applications
From machinery components to infrastructural elements, various industrial products utilize injection molding to ensure durability and reliability.
Integration with Metal Fabricators
As a key player in the metal fabricators category, injection plastic molding can complement metal components. This synergy is essential for creating hybrid products that leverage the strengths of both materials.
Examples of Collaboration
- Composite Parts: Metal and plastic combinations can enhance strength while reducing weight.
- Over-Molding: Metal inserts can be over-molded with plastic to improve functionality and performance.
Choosing the Right Manufacturing Partner
When seeking a partner for injection plastic molding, consider companies like DeepMould. Their expertise in crafting high-quality plastic components makes them a reliable choice in the industry.
Factors to Consider
Choosing the right provider involves evaluating:
- Experience and Expertise: Look for a company with a proven track record in injection molding.
- Technology and Equipment: Advanced machinery aids in achieving precision and efficiency.
- Material Selection: A diverse range of plastic materials allows for versatile production capabilities.
- Customer Support: Responsive and knowledgeable support can enhance collaboration.
Future Trends in Injection Plastic Molding
The landscape of injection plastic molding is ever-evolving, with several trends shaping its future:
Sustainability Initiatives
As environmental concerns grow, more companies are adopting sustainable practices. This includes using recycled materials and optimizing energy consumption during the molding process.
Smart Manufacturing
Integration of IoT (Internet of Things) in injection molding facilities is on the rise. This technology enhances monitoring and maintenance, leading to increased efficiencies.
Advanced Materials
The development of new materials, such as biodegradable plastics and composites, is expanding the capabilities and applications of injection molding.
Conclusion
In summary, injection plastic molding is a cornerstone of modern manufacturing, delivering exceptional precision, cost-effectiveness, and versatility across various industries. Its integration with metal fabrication opens new avenues for product development, driving innovation and efficiency. As trends towards sustainability and smart manufacturing continue to shape the industry, companies that embrace these changes will lead the way forward. For those looking to harness the power of injection molding, choosing a competent and experienced partner like DeepMould is invaluable.